Direct Thermochemical Liquefaction
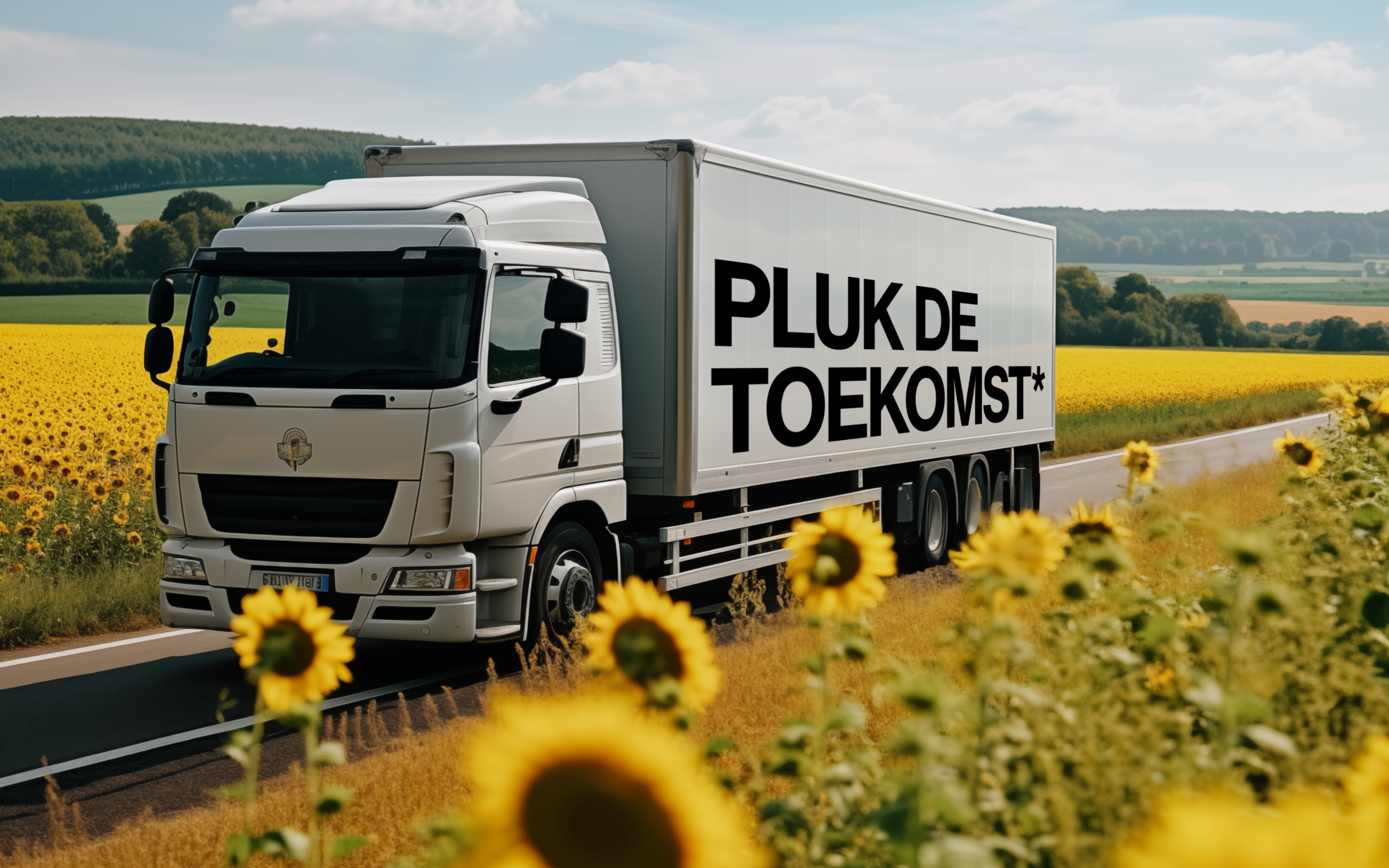
The new IEA Bioenergy Task 34 report "Direct Thermochemical Liquefaction - Characteristics, processes and technologies" summarises the current state, recent advances and perspectives in biofuel production via direct thermochemical liquefaction (DTL).
The report begins with detailing the difference between direct and indirect liquefaction: Direct liquefaction produces liquid bio-crude oil in one step, whereas indirect liquefaction employs a preceding gasification step, which then allows for gas-to-liquid conversions afterwards. Subsequently, the underlying principles of biomass depolymerisation are briefly explained, being ordered by temperature into biological, chemical, or thermal principles. The main difference of thermal decomposition (starting at temperatures of 250 °C) to the other two principles lies in the full decomposition of all the biomass, including the heat-resistant lignin. Consequently, thermal degradation is less feedstock-specific than biological or chemical processes and thus seen as more robust towards variations in feedstock, with the additional advantage of intrinsically avoiding the use of auxiliary chemicals.
The report continues with a description of the three most prevalent DTL processes, namely fast pyrolysis, solvolysis and hydrothermal liquefaction (HTL). In fast pyrolysis, dry conditions are chosen such that all inherent water directly vaporises. Gaseous reactions from volatiles dominate and result in pyrolysis. In thermodynamic equilibrium, this reaction would only result in gaseous and solid products, which is why the released volatiles need to be condensed quickly (hence the name "fast" pyrolysis), producing bio-oil within only a few seconds of residence time.
In solvolysis, the degradation reactions in a liquid solvent dominate. If the solvent is organic, it can additionally donate hydrogen to the decomposition intermediates. The exact solvent in use defines the range of possible decomposition reactions and therefore the composition of the final product phase. If the liquid solvent is aqueous (thus requiring high pressure), the process is called HTL. Since water promotes hydrolysis of cellulose and hemicellulose, the medium becomes a desired reactant. In contrast to pyrolysis, the formation of solids is mostly prevented and much lower temperatures are needed. The resulting product differs in that it contains almost no sugars and a higher amount of phenols.
After explaining the different ways to obtain bio-crude oil, the report continues with the depiction of refining (i.e. upgrading) the bio-crude towards higher-value biofuels. Due to the related costs, "bio-oil should be upgraded as little as possible but as much as required for the intended application". As post-treatment steps of DTL, filtering out any remaining solid particles or blending the bio-oil with other liquids to achieve desired properties (such as viscosity) are common. The "most widely discussed" upgrading possibility of bio-crude oil is catalytic hydrotreatment, or hydrodeoxygenation (HDO), aiming to reduce the typically high oxygen fraction from the bio-oil. HDO can also be applied during fast pyrolysis, either in-situ (catalytic fast pyrolysis) or ex-situ before condensation. In-situ upgrading is particularly interesting for solvolysis in organic solvents. One can differentiate between mild HDO and deep HDO, with the former aiming to improve and stabilise pyrolysis oil and the latter aiming to produce purer mixtures of hydrocarbons.
The resulting DTL bio-oils differ noticeably from fossil fuels as they contain a small percentage of solids (as opposed to none for fossil fuels), potentially more ash, less nitrogen and sulphur, a considerable amount of water (3-30 %) and a significantly higher amount of oxygen due to the water and oxygenated organic compounds, leading to a lower heating value. Fast pyrolysis oil is suspect to "aging" reactions due to its chemical instability, and since elevated temperatures accelerate aging they cannot be distilled. Bio-crude from HTL and solvolysis using organic solvents displays a much lower oxygen content than pyrolysis oil and a much lower water content, leading to higher energy densities but coming at the expense of high viscosities, "even compared to heavy fuel oil".
Finally, perspectives of DTL are mentioned. While pyrolysis currently used for producing heating oil, higher value applications exist but do not experience the same growth due to the low price of fossil counterparts in our current policy framework. Furthermore, more research is needed in utilising feedstocks other than wood (residues). Solvolysis with organic solvents is ongoing R&D work, with the challenges to ensure a stable solvent phase, maximise recovery of bio-crude (possibly via distillation) and treat the aqueous phase with heavy organic load. HTL advanced promisingly over the past decades, with industrial scale up demonstration plant being built. Similar to pyrolysis, high value use of the obtained bio-crude requires more research, as well as the pumps to ensure a feed of stable slurry against the high reactor pressures and the efficient separation of bio-crude from the aqueous phase. It should also be mentioned that all DTL processes produce a bio-crude that differs in composition from fossil oil, therefore requiring the need of better characterisation and creating new standards for "a well-defined marketable product".
Recente artikelen
Brito: Multipurpose integrated development of biomass resources - A strategic solution for energy production and environmental management | 2015
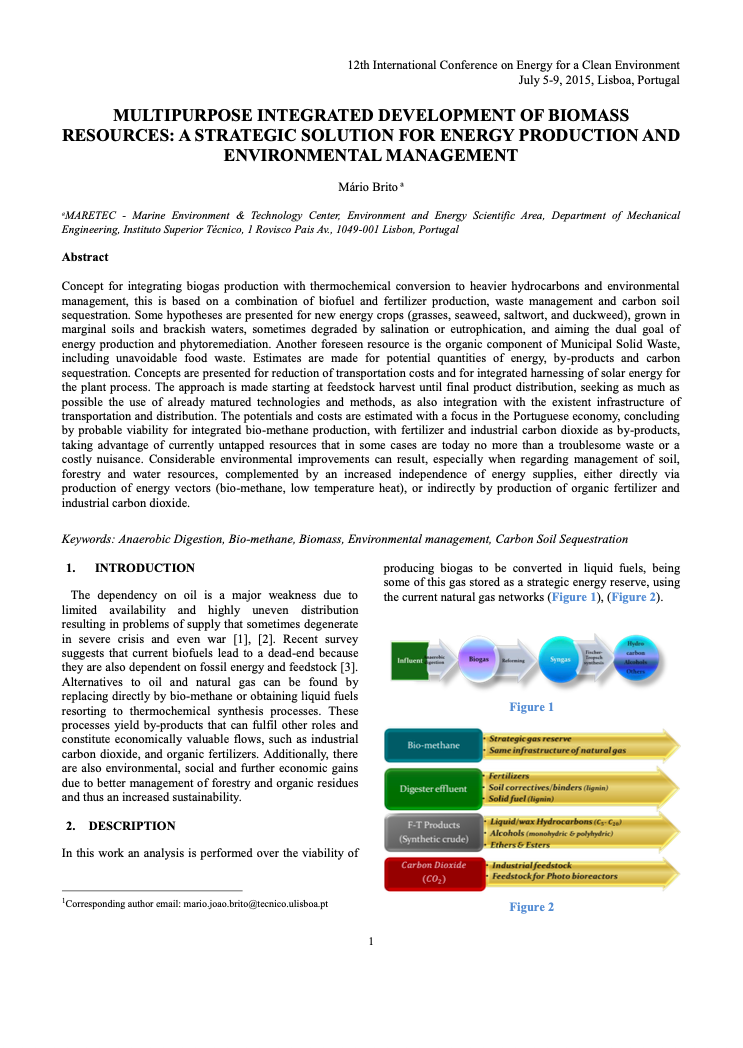
Retrospective on Public Seminar: The new feedstock producers for a fossil free chemical industry | December 10, 2024
Voelker et al.: Towards carbon-neutral and clean propulsion in heavy-duty transportation with hydroformylated Fischer–Tropsch fuels | 2024
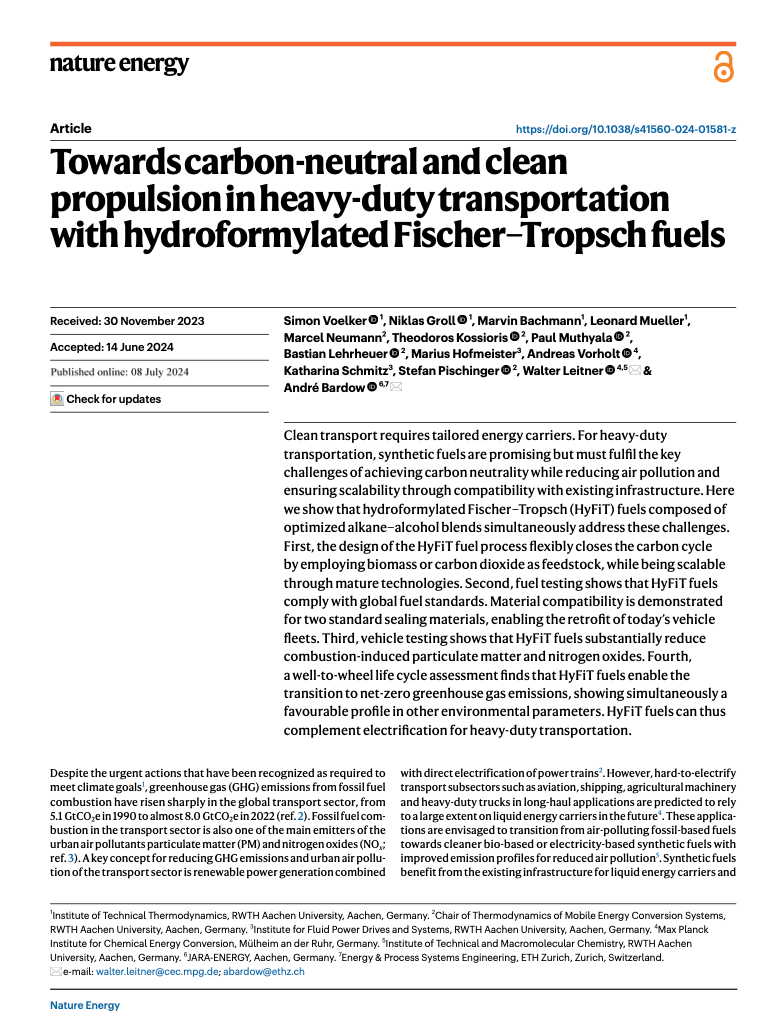